Collaboration key in addressing skills loophole
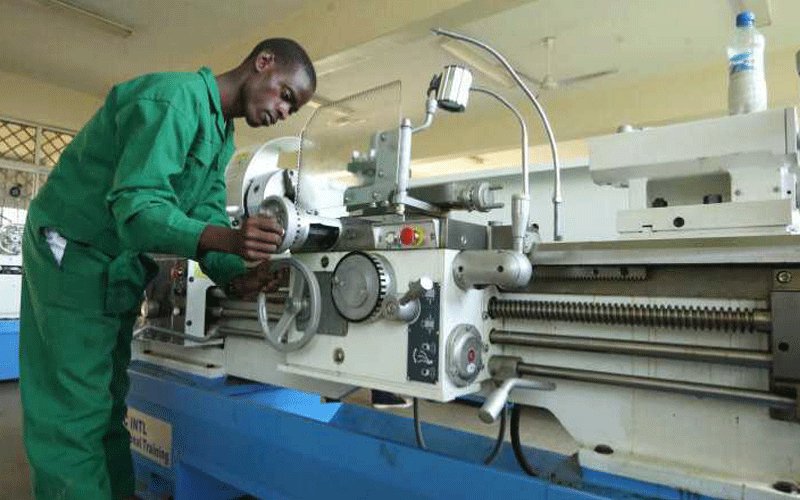
Today’s world of work is changing rapidly, with new jobs emerging and existing jobs evolving on a regular basis.
Technical innovations under Industry 4.0 are driving the demand for new skills as more industries shift to automation and artificial intelligence.
Manufacturers are now, more than ever, keeping abreast and adopting technical innovations that improve efficiency, to remain competitive in the global markets.
Industry remains a big contributor to job creation. To sustain this reality, there is huge demand for skilled workers in industries in Kenya, as well as a demand for improved quality of goods and services that meet both local and international standards.
However, there is a mismatch of skills taught in Technical and Vocational Education and Training (TVET) institutions and those required in industry.
A survey by Deloitte and The Manufacturing Institute, indicates that as digital transformation in industry continues to develop, skills needed in smart factories will be different.
The survey, further notes that the workforce does not possess many of these skills. This is a concern that Kenyan manufacturers have raised.
Lack of such skills results in high labour costs, slow adoption of technology, minimal knowledge transfer and ultimately, high unemployment levels, particularly for technology-intensive sectors, hence threatening the achievement of our economic agenda.
Kenya Association of Manufacturers (KAM) acknowledges this need. Through its TVET programme, the Association seeks to address the skills gap manufacturers are grappling with.
The focus on technical training stems from the large number of technicians that industry takes in, based on the shop floor needs.
A secure future for the manufacturing sector starts with today’s students and workforce.
Emerging technologies and the ever-changing market demands require us to stay ahead of the curve to bridge the current and upcoming skills gap. How do we achieve this?
The skills gap challenge calls for stronger collaboration between relevant partners and stakeholders.
Collaborative investments in technical and vocational education and training (TVET) are resulting in enhanced employability skills for youth in Kenya.
KAM is actively involved in the ‘promotion of youth employment and vocational training’ programme, implemented through the Deutsche Gesellschaft für Internationale Zusammenarbeit (GIZ) GmbH.
In close cooperation with training institutions, industry is creating linkages for trainees in selected vocations to learn through a structured and practical in-company training experience.
This cooperative vocational training approach is modelled on the German Dual Vocational Training that has powered Germany’s growth and industrialisation for over a century.
The approach entails working with industries, TVET institutions and government agencies to develop and deliver a training that allows graduates to be placed on a structured on-the-job mentorship in industries where they gain practical employability skills.
The piloting of the cooperative approach has increased engagement of industry to improve the content and quality of training delivery for and manufacturing sectors.
Partnerships between stakeholders in the TVET space have been enhanced, with increased responsiveness to new technologies.
So far, students have had a three-month training block (semester) in industry after the first block in class, providing hands on experience on their learning experience.
Industry within the sector holds continuous engagement with training institutions, advising on learning outcomes and how to best achieve them both in class and in industry.
It is undeniable that investments in vocational training must go beyond effective policies, provision of training materials and the review and improvement of training curricula.
We urge industries to support more practical training experience in a variety of occupational areas in order to build the workforce of the future. —The writer is chief executive of KAM ceo@kam.co.ke.