New threshing technology to ease finger millet grain preparation pain
By Wahinya Henry, May 18, 2021
Farmers, who have long shied away from growing the crop due to its labour-intensive nature are now embracing the venture, thanks to a newly developed machine that threshes, winnows and polishes the crop’s dry panicles saving them time, reduce wastage and promising good returns.
Four years ago, Jane Cheboi decided to grow finger millet on part of their six-acre family land in Sendent village, Bomet County to earn much needed income before maize harvest season.
However, despite good yields, she endured the challenges of manually threshing the millet. “Many are the times I thought of giving up,” she recounts.
Now, she is one of the rising number of farmers in Kenya whose hustle of threshing millet is set to end following the development of a machine to do the job.
The grain does not only better meet nutritional needs for consumers, but also fulfills economic and agronomic requirements at a time of climate change.
Much-needed innovation
Traditionally, harvesting of millet is done by removing the individual heads of the crop with sickles or small hand knives.
This is sometimes preceded by breaking the stems. The edible grains are then separated from the loose branching cluster of millet flowers known as panicles, which is a quite tedious process as it involves putting sizeable amount of dried finger millet in bags, beating to detach grains, repeated winnowing to obtain clean grains and packaging.
“The finger millet thresher has proven to be an ideal solution to the manual threshing of finger millet,” says Prof Christopher Kanali, an associate lecturer at Jomo Kenyatta University of Agriculture and Technology (JKUAT) and an expert in processing of agricultural materials.
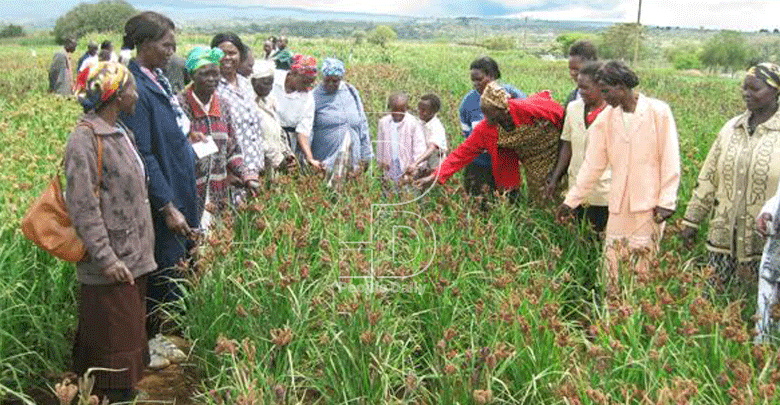
The innovation is a joint product of JKUAT and Kenya Agricultural and Research Organisation (KALRO), which wanted to solve problems facing farmers in Bomet and Kericho counties before upscaling their operations to other finger millet growing counties.
The machine, which is made of mild steel, a component readily available locally, is portable making it easier to be moved from site to site.
It also has a hopper (an inlet where the finger millet is put) with a dimension of 1,650milimetres in length, width of 900 milimetres and height if 1,550 milimetres (height of 1,130 milimetres with the hopper detached).
Reduce post-harvest loss
It has the ability to thresh, winnow and polish dry finger millet pinnacles, and is operated by two people.
It has a 98 per cent removal of bran on the grain tips as well as 95 per cent of chaff, runs on a petrol engine with 7.5 horsepower and can produce between 200 and 300 kilogrammes per hour of clean finger millet.
According to Prof Kanali, the 150-kilogramme machine consumes about one litre of petrol per hour and costs roughly between Sh180,000 and Sh250,000.
On capacity building, the JKUAT team and partners embarked on a series of field demonstrations in various farms in the two counties in a bid to reduce post-harvest loss and ease the threshing process.
He has called upon county governments to set up funding for farmers to be able to acquire the machine as it is costly.
Prof Kanali further encouraged farmers to form groups and pool resources together to increase their purchasing power.
“We have the capacity and skills to address problems facing us as well as come up with innovations in the long-term, especially in the agricultural sector. Research is key if we are able to leverage on it fully,” he said.
Also involved in the machine development are Dr Erick Ronoh as the project secretariat, Gerishom Andalia and Victor Lang’at who are technical field assistants.